3D Printing vs Traditional Manufacturing: Pros and Cons
In the world of manufacturing, two distinct approaches dominate: 3D printing and traditional manufacturing. While both serve the same goal of creating physical products, their methods and the resulting benefits differ greatly. As 3D printing continues to advance, many businesses are considering whether this cutting-edge technology can replace traditional manufacturing techniques. In this post, we’ll dive into the pros and cons of 3D printing and traditional manufacturing, helping you understand the strengths and limitations of each method to make an informed decision for your production needs.
What is Traditional Manufacturing?
Traditional manufacturing includes a wide range of methods, such as casting, molding, machining, milling, and lathe work. These processes typically involve cutting, shaping, or assembling raw materials into finished products. The most common forms of traditional manufacturing involve subtractive methods (removing material) or formative methods (shaping material using molds or dies).
What is 3D Printing?
3D printing, or additive manufacturing, is the process of creating objects layer by layer based on a digital model. Unlike traditional manufacturing, which typically involves subtracting material from a larger block, 3D printing adds material in precise amounts to form the desired shape.
Pros of 3D Printing
1. Design Flexibility and Complexity
Advantages:
3D printing allows for the creation of highly complex, intricate designs that would be impossible or prohibitively expensive to produce using traditional methods. It enables customization and rapid prototyping without the need for expensive molds or tooling.
- Prototyping Speed: 3D printing accelerates the prototyping process. You can quickly make adjustments to designs and produce working models, which is ideal for iterative design and custom solutions.
- Complex Geometries: Intricate geometries, such as organic shapes, lattices, and interlocking parts, are easier to design and manufacture with 3D printing, offering unparalleled creative freedom.
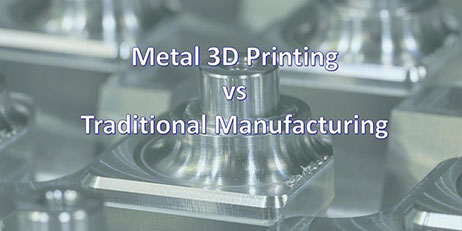
2. Reduced Material Waste
Advantages:
Since 3D printing adds material layer by layer, it minimizes waste compared to traditional subtractive manufacturing methods, which often involve cutting away excess material. This makes 3D printing more eco-friendly and cost-effective in terms of material usage.
- Material Efficiency: Materials like plastics, metals, and composites are used precisely where needed, reducing overall consumption.
- Recycling and Sustainability: Many 3D printing processes allow for the use of recycled materials, further contributing to sustainability.
3. Lower Setup Costs
Advantages:
Traditional manufacturing often requires the creation of specialized molds or tooling, which can be expensive and time-consuming. In contrast, 3D printing eliminates these setup costs because it doesn’t require the creation of custom molds or dies for production.
- No Need for Tooling: There’s no need for expensive molds, dies, or fixtures, making it ideal for low-volume and custom production.
- On-Demand Manufacturing: 3D printing allows for on-demand, small-batch production, which eliminates the need for bulk production and inventory storage.
4. Faster Time-to-Market
Advantages:
The speed of 3D printing makes it easier and faster to bring a product to market. Since designs can be tested and modified quickly, businesses can respond faster to market demands and customer feedback.
- Rapid Prototyping: Changes can be made to the digital model and printed immediately, significantly reducing the time it takes to create prototypes and test new ideas.
- Shorter Production Lead Times: Once the design is finalized, 3D printers can begin creating parts immediately, streamlining the production timeline.
Cons of 3D Printing
1. Limited Material Options
Disadvantages:
Although 3D printing has evolved to include a variety of materials, it still doesn’t match the range of materials available in traditional manufacturing, especially for industrial-grade products.
- Material Strength: While metals and polymers are available, 3D printing materials may not always meet the strength, durability, and finish quality of materials used in traditional manufacturing processes like forging or injection molding.
- Limited Range of Materials: High-performance materials, such as those used in aerospace or automotive industries, are still relatively rare and expensive in 3D printing.
2. Slower Production Speeds for Large Volumes
Disadvantages:
While 3D printing is fast for prototyping and small batches, it is not always as efficient as traditional manufacturing for large-volume production runs. The layer-by-layer process can take significantly longer compared to methods like injection molding or stamping.
- Inefficiency for Mass Production: When manufacturing large quantities of identical products, traditional manufacturing methods can be much faster and more cost-effective.
- Longer Printing Times: For larger or more complex parts, 3D printing may require extended production times.
3. Limited Surface Finish and Resolution
Disadvantages:
While 3D printing can produce highly detailed designs, the surface finish and resolution may not always meet the desired quality for certain applications, especially for parts that require smooth, high-quality finishes.
- Post-Processing Required: Parts often require post-processing steps, such as sanding, smoothing, or coating, to achieve the desired finish.
- Layer Visibility: The layer-by-layer nature of 3D printing can sometimes result in visible lines or imperfections on the surface, which may not be acceptable for high-end applications.
Pros of Traditional Manufacturing
1. High-Volume Production
Advantages:
Traditional manufacturing methods, such as injection molding or stamping, are highly efficient for mass production, allowing manufacturers to produce thousands or millions of identical parts at a fast rate.
- Efficiency for Large Batches: Once the tooling is set up, traditional manufacturing processes are optimized for producing large quantities with minimal labor and downtime.
- Consistency: Traditional manufacturing methods provide consistency in product quality, which is crucial for mass-produced items.
2. Material Versatility
Advantages:
Traditional manufacturing offers a wider selection of materials, including metals, alloys, plastics, and composites, many of which are more durable and cost-effective for certain types of production.
- Material Strength: Materials used in traditional manufacturing are often stronger and more durable, making them suitable for heavy-duty, high-performance applications.
- High-Quality Finishes: Traditional methods can achieve smoother surface finishes without the need for post-processing.
Cons of Traditional Manufacturing
1. High Setup Costs
Disadvantages:
The need for expensive molds, dies, and tooling makes traditional manufacturing methods costly to set up. These upfront costs can be prohibitive for small runs or custom designs.
- Long Lead Times: Setting up tooling and molds can take a significant amount of time, delaying production and increasing overall costs.
- Tooling Wear: Tools and molds wear down over time and need to be replaced, adding to the maintenance costs.
2. Limited Design Flexibility
Disadvantages:
Traditional manufacturing methods often have limitations when it comes to producing complex, customized designs. Parts that require intricate geometry or custom features can be difficult or impossible to create without significant retooling.
- Design Restrictions: Some shapes or geometries, such as internal cavities or organic curves, are hard to achieve with traditional methods without adding additional steps.
Conclusion
The debate between 3D printing and traditional manufacturing ultimately comes down to the specific needs of the project at hand. For custom, low-volume production or rapid prototyping, 3D printing offers unique advantages, such as flexibility, reduced waste, and faster time-to-market. However, for high-volume production or parts requiring superior strength and finish, traditional manufacturing remains the best choice.
In many industries, the future of manufacturing may not lie in one or the other but in the combination of both, where 3D printing and traditional methods complement each other, creating a more efficient and versatile manufacturing process. Understanding the strengths and limitations of each will help businesses select the right approach for their needs.