Troubleshoot Common 3D Printing Problems
3D printing can be exciting, but challenges are inevitable. From filament jams to layer shifts, many issues can occur. Here’s a guide to troubleshooting common 3D printing problems and improving your print quality.
1. Prints Not Sticking to the Bed
Problem: The first layer doesn’t adhere to the print bed, causing failed prints.
Solution:
- Ensure the print bed is level. Use a leveling tool or manual adjustments for precision.
- Clean the bed surface with isopropyl alcohol to remove dust or oils.
- Increase bed temperature slightly or apply adhesives like glue sticks or painter’s tape.
- Check the nozzle height; it should be close enough for proper adhesion but not too close to block extrusion.
2. Warping
Problem: The base of the print lifts off the bed, distorting the shape.
Solution:
- Use a heated bed and ensure it’s set to the correct temperature for your material.
- Enable a brim or raft in your slicer settings to improve stability.
- Reduce cooling fan speed for the first few layers to maintain temperature.
- Print in an enclosed chamber to minimize drafts and temperature fluctuations.
3. Stringing or Oozing
Problem: Thin strands of filament form between parts of the print.
Solution:
- Enable retraction settings in your slicer to pull filament back when the nozzle moves.
- Reduce print temperature slightly to prevent filament from melting excessively.
- Increase travel speed to minimize oozing during movement.
- Check the nozzle for clogs or damage that could worsen stringing.
4. Layer Shifting
Problem: Layers misalign, causing the print to look uneven or skewed.
Solution:
- Tighten belts and ensure the pulleys are securely fastened to prevent movement slippage.
- Check that the stepper motors are functioning properly and not overheating.
- Reduce print speed to minimize vibrations affecting layer placement.
- Verify the printer’s frame is stable and level.
5. Under-Extrusion
Problem: The printer produces thin or incomplete layers.
Solution:
- Ensure the nozzle is clean and not partially clogged.
- Verify that the filament diameter matches the slicer settings.
- Check the extruder gear for debris or improper tension.
- Increase the extrusion multiplier in your slicer if needed.
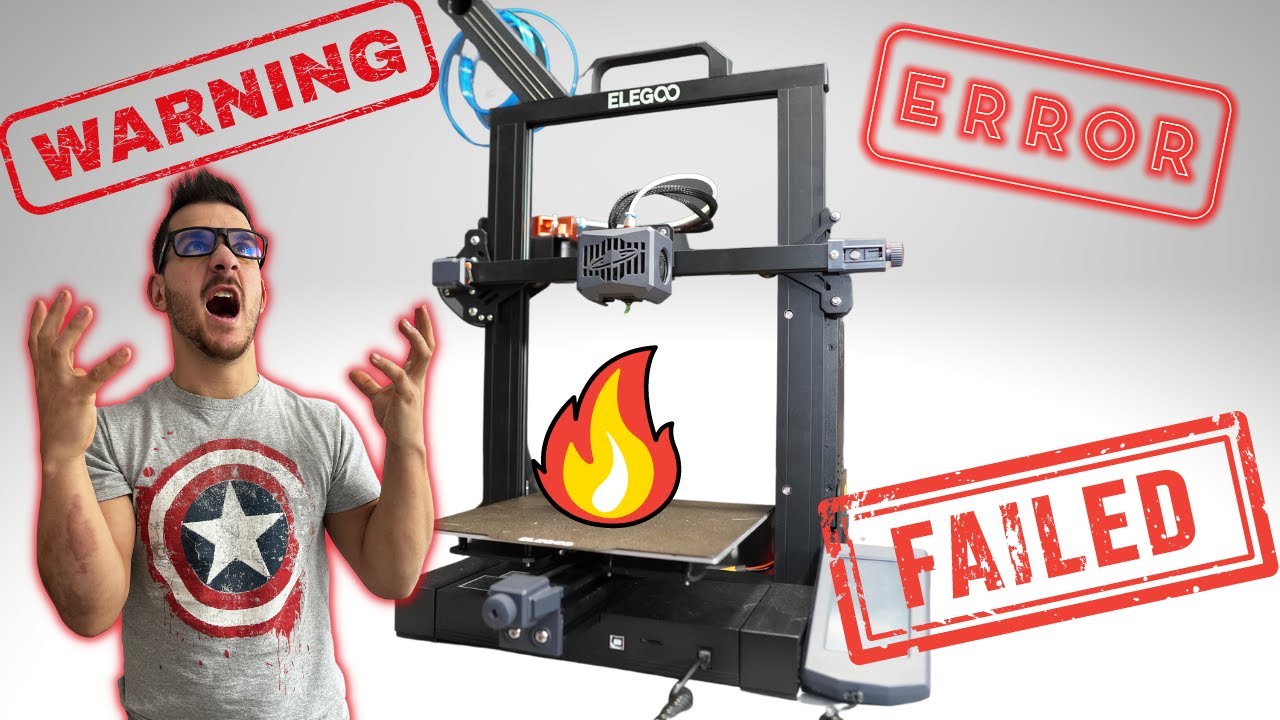
6. Over-Extrusion
Problem: Too much filament is extruded, causing blobs or ridges on the print.
Solution:
- Reduce the extrusion multiplier or flow rate in your slicer.
- Confirm that the nozzle diameter matches the slicer’s settings.
- Lower the print temperature to avoid excessive filament flow.
7. Filament Jams
Problem: Filament gets stuck in the extruder, halting the print.
Solution:
- Remove the filament and clean the nozzle with a cleaning needle or cold-pull method.
- Check for debris in the extruder gear.
- Use high-quality filament to avoid inconsistent thickness or impurities.
- Maintain proper storage to prevent moisture from affecting the filament.
8. Cracks in Tall Prints
Problem: Vertical cracks form in prints, especially with taller models.
Solution:
- Increase the nozzle temperature slightly to improve layer bonding.
- Decrease cooling fan speed for better adhesion between layers.
- Use an enclosure to keep the environment warm and stable.
9. Ghosting or Ringing
Problem: Echo-like lines appear around the edges of the print.
Solution:
- Reduce print speed to minimize vibrations.
- Tighten the printer’s frame and ensure all bolts are secure.
- Lower acceleration and jerk settings in your slicer.
- Check that belts and pulleys are tight and in good condition
Final Thoughts
3D printing requires patience and practice. By identifying and addressing these common issues, you’ll achieve better results and enjoy a smoother printing experience. Regular maintenance and adjustments are key to consistent success.